Birth of the LNF
#1
Birth of the LNF
Old Redline forum thread back in 2006. Lots of good info and pics!
Can't post link here to due software block. Just take out the *>>>* then add last line provided and paste into address bar
http://>>>>www.>>>red>>>>line>>forums.com
/forums/sky-discussion/18110-2-0-lnf-sidi-engine-control.html
Turbocharger Description and Operation
A turbocharger is a compressor that is used to increase the power output of an engine by increasing the mass of the oxygen and therefore the fuel entering the engine. This BorgWarner™ dual-scroll turbocharger is mounted on the exhaust manifold and the lightweight turbine is driven by the waste energy generated by the flow of the exhaust gases. The turbine is connected by a shaft to the compressor which is mounted in the induction system of the engine. The compressor vanes compress the intake air above atmospheric pressure, thereby greatly increasing the density of the air entering the engine. The turbocharger is capable of producing up to 20 psi, 1.40 bar, of power-enhancing boost.
The turbocharger incorporates a wastegate that is controlled by a pressure differential, that is determined by the engine control module (ECM) by means of a PWM solenoid, in order to regulate the pressure ratio of the compressor. A compressor bypass valve also controlled by the ECM by utilizing a remotely mounted solenoid is integrated into the unit to prevent compressor surging and damage from vibrations by opening during abrupt closed throttle conditions. When the valve is open during closed throttle deceleration conditions, the bypass valve allows the air to recirculate in the turbocharger and maintain compressor speed. Within a calibrated range during the closed throttle event, or upon a wide open throttle command the valve will then close to optimize turbo response.
The turbocharger is connected to the engine oiling system by a supply and drain tube and Mobil 1™ synthetic oil is installed at the factory. Synthetic oil is required for its friction-reducing capabilities and high-temperature performance. There is a cooling system circuit in the turbocharger that utilizes the engine coolant to further reduce operating temperatures.
Intercooler Description
The turbocharger is supported by an air-to-air intercooler system, which uses fresh air drawn through a heat exchanger to reduce the temperature of the warmer compressed air forced through the intake system. Inlet air temperature can be reduced by up to 100°C (180°F), enhancing performance because cooler air is denser in oxygen and promotes optimal combustion. The intercooler is connected to the turbocharger and to the throttle body by flexible ductwork that requires the use of special high torque fastening clamps.
High Pressure Fuel Pump
The high pressure fuel pump is a mechanical one cylinder design driven by an additional three lobe cam on the camshaft. High pressure fuel is regulated by the fuel rail pressure (FRP) regulator, which is a part of the high pressure fuel pump. The FRP regulator is a magnetic actuator which controls the inlet valve of the high pressure pump. The ECM provides battery voltage on the actuator hi circuit and ground on the actuator low circuit. Both circuits are controlled through output drivers within the ECM. When deactivated, both drivers are disabled and the inlet valve is held open with spring pressure. When activated, the actuator low circuit driver connects the low circuit to ground and the actuator hi circuit driver pulse-width modulates (PWM) the hi circuit. The ECM uses the camshaft and crankshaft position sensor inputs to synchronize the FRP regulator with the position of each of the three camshaft lobes. The ECM regulates fuel pressure by adjusting the portion of each pump stroke that provides fuel to the rail. The high pressure fuel pump also contains an integrated pressure relief valve.
Fuel Rail Assembly
The fuel rail assembly attaches to the cylinder head. The fuel rail distributes high pressure fuel to the fuel injectors. The fuel rail assembly consists of the following components:
• The direct fuel injectors
• The fuel rail pressure (FRP) sensor
Fuel Injectors
The fuel injection system is a high pressure, direct injection, returnless on-demand design. The fuel injectors are mounted in the cylinder head beneath the intake ports and spray fuel directly into the combustion chamber. Direct injection requires high fuel pressure due to the fuel injector's location in the combustion chamber. Fuel pressure must be higher than compression pressure requiring a high pressure fuel pump. The fuel injectors also require more electrical power due to the high fuel pressure. The ECM supplies a separate high voltage supply circuit and a driver circuit for each fuel injector.
The fuel injector assembly is an inside opening electrical magnetic injector. The injector has six precision machined holes that generate a cone shaped oval spray pattern. The fuel injector has a slim extended tip in order to allow a sufficient cooling jacket in the cylinder head.
Fuel Injection Fuel Rail Fuel Pressure Sensor
The fuel rail pressure sensor detects fuel pressure within the fuel rail. The engine control module (ECM) provides a 5 volt reference voltage on the 5 volt reference circuit and ground on the reference ground circuit. The ECM receives a varying signal voltage on the signal circuit. The ECM monitors the voltage on the FRP sensor circuits. When the fuel pressure is high, the signal voltage is high. When the fuel pressure is low, the signal voltage is low.
The fuel pressure will vary from approximately 752 psi (50 bar) at idle to 2,276 psi (150 bar) of pressure at wide-open throttle during maximum boost

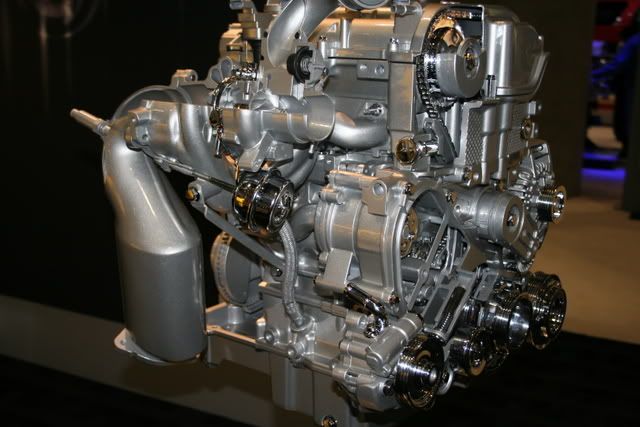
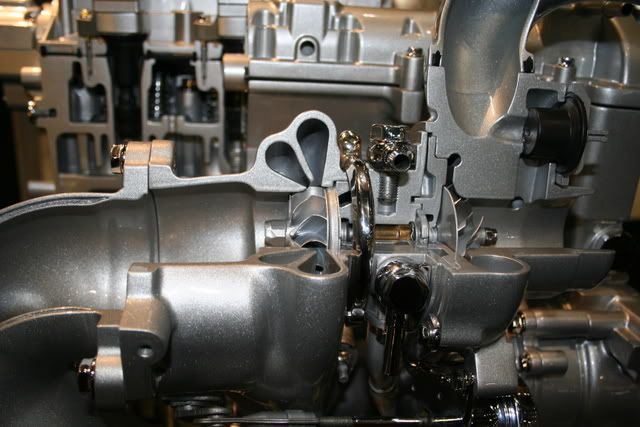
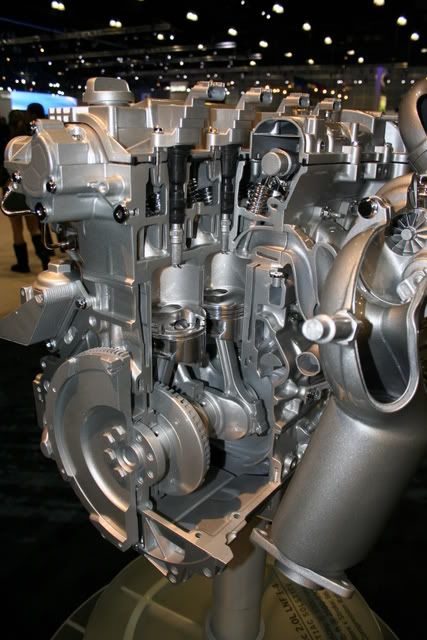
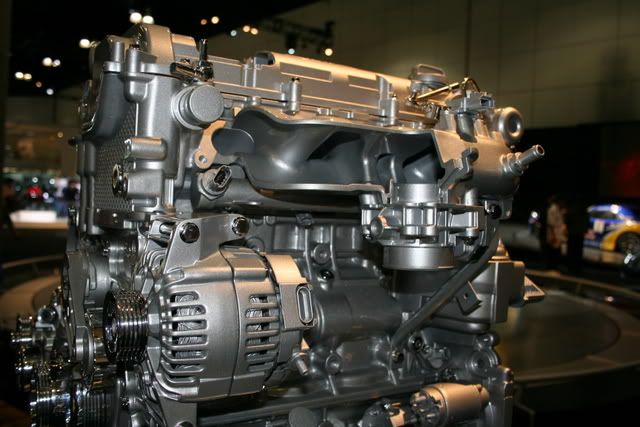
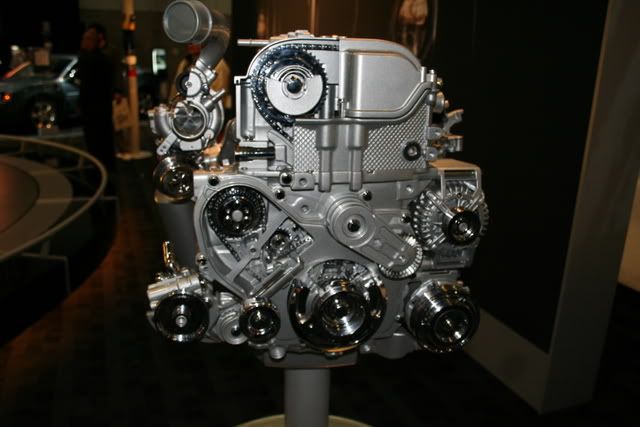

Can't post link here to due software block. Just take out the *>>>* then add last line provided and paste into address bar

http://>>>>www.>>>red>>>>line>>forums.com
/forums/sky-discussion/18110-2-0-lnf-sidi-engine-control.html
Turbocharger Description and Operation
A turbocharger is a compressor that is used to increase the power output of an engine by increasing the mass of the oxygen and therefore the fuel entering the engine. This BorgWarner™ dual-scroll turbocharger is mounted on the exhaust manifold and the lightweight turbine is driven by the waste energy generated by the flow of the exhaust gases. The turbine is connected by a shaft to the compressor which is mounted in the induction system of the engine. The compressor vanes compress the intake air above atmospheric pressure, thereby greatly increasing the density of the air entering the engine. The turbocharger is capable of producing up to 20 psi, 1.40 bar, of power-enhancing boost.
The turbocharger incorporates a wastegate that is controlled by a pressure differential, that is determined by the engine control module (ECM) by means of a PWM solenoid, in order to regulate the pressure ratio of the compressor. A compressor bypass valve also controlled by the ECM by utilizing a remotely mounted solenoid is integrated into the unit to prevent compressor surging and damage from vibrations by opening during abrupt closed throttle conditions. When the valve is open during closed throttle deceleration conditions, the bypass valve allows the air to recirculate in the turbocharger and maintain compressor speed. Within a calibrated range during the closed throttle event, or upon a wide open throttle command the valve will then close to optimize turbo response.
The turbocharger is connected to the engine oiling system by a supply and drain tube and Mobil 1™ synthetic oil is installed at the factory. Synthetic oil is required for its friction-reducing capabilities and high-temperature performance. There is a cooling system circuit in the turbocharger that utilizes the engine coolant to further reduce operating temperatures.
Intercooler Description
The turbocharger is supported by an air-to-air intercooler system, which uses fresh air drawn through a heat exchanger to reduce the temperature of the warmer compressed air forced through the intake system. Inlet air temperature can be reduced by up to 100°C (180°F), enhancing performance because cooler air is denser in oxygen and promotes optimal combustion. The intercooler is connected to the turbocharger and to the throttle body by flexible ductwork that requires the use of special high torque fastening clamps.
High Pressure Fuel Pump
The high pressure fuel pump is a mechanical one cylinder design driven by an additional three lobe cam on the camshaft. High pressure fuel is regulated by the fuel rail pressure (FRP) regulator, which is a part of the high pressure fuel pump. The FRP regulator is a magnetic actuator which controls the inlet valve of the high pressure pump. The ECM provides battery voltage on the actuator hi circuit and ground on the actuator low circuit. Both circuits are controlled through output drivers within the ECM. When deactivated, both drivers are disabled and the inlet valve is held open with spring pressure. When activated, the actuator low circuit driver connects the low circuit to ground and the actuator hi circuit driver pulse-width modulates (PWM) the hi circuit. The ECM uses the camshaft and crankshaft position sensor inputs to synchronize the FRP regulator with the position of each of the three camshaft lobes. The ECM regulates fuel pressure by adjusting the portion of each pump stroke that provides fuel to the rail. The high pressure fuel pump also contains an integrated pressure relief valve.
Fuel Rail Assembly
The fuel rail assembly attaches to the cylinder head. The fuel rail distributes high pressure fuel to the fuel injectors. The fuel rail assembly consists of the following components:
• The direct fuel injectors
• The fuel rail pressure (FRP) sensor
Fuel Injectors
The fuel injection system is a high pressure, direct injection, returnless on-demand design. The fuel injectors are mounted in the cylinder head beneath the intake ports and spray fuel directly into the combustion chamber. Direct injection requires high fuel pressure due to the fuel injector's location in the combustion chamber. Fuel pressure must be higher than compression pressure requiring a high pressure fuel pump. The fuel injectors also require more electrical power due to the high fuel pressure. The ECM supplies a separate high voltage supply circuit and a driver circuit for each fuel injector.
The fuel injector assembly is an inside opening electrical magnetic injector. The injector has six precision machined holes that generate a cone shaped oval spray pattern. The fuel injector has a slim extended tip in order to allow a sufficient cooling jacket in the cylinder head.
Fuel Injection Fuel Rail Fuel Pressure Sensor
The fuel rail pressure sensor detects fuel pressure within the fuel rail. The engine control module (ECM) provides a 5 volt reference voltage on the 5 volt reference circuit and ground on the reference ground circuit. The ECM receives a varying signal voltage on the signal circuit. The ECM monitors the voltage on the FRP sensor circuits. When the fuel pressure is high, the signal voltage is high. When the fuel pressure is low, the signal voltage is low.
The fuel pressure will vary from approximately 752 psi (50 bar) at idle to 2,276 psi (150 bar) of pressure at wide-open throttle during maximum boost

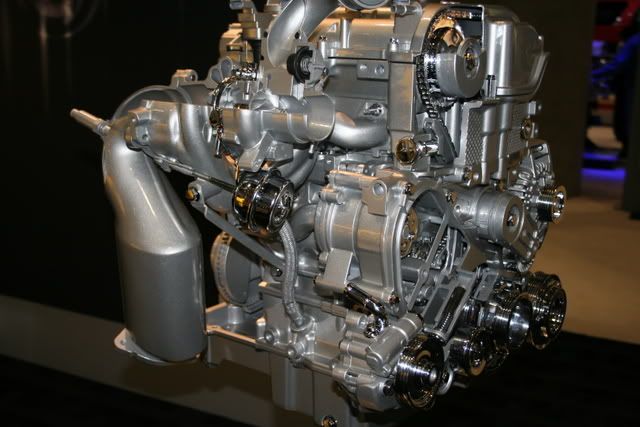
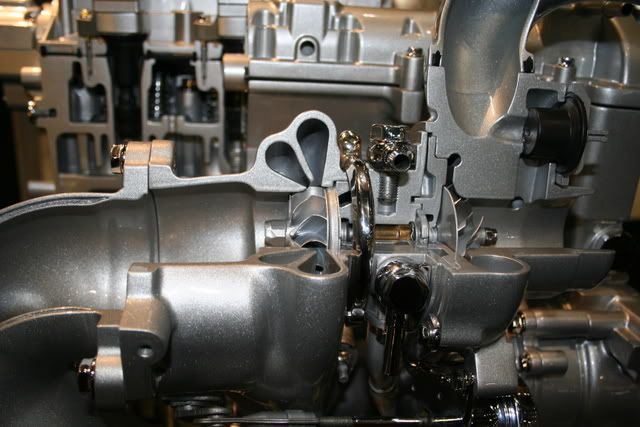
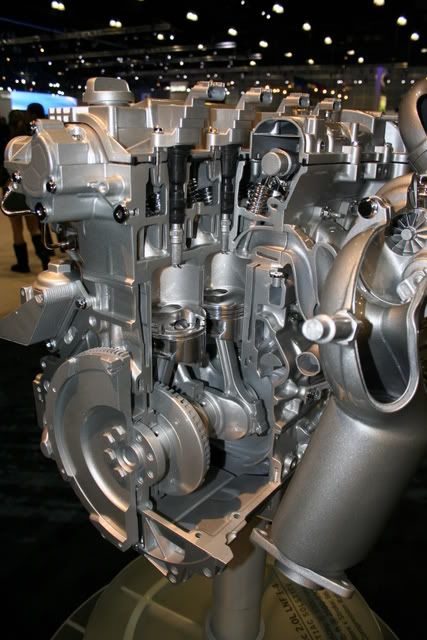
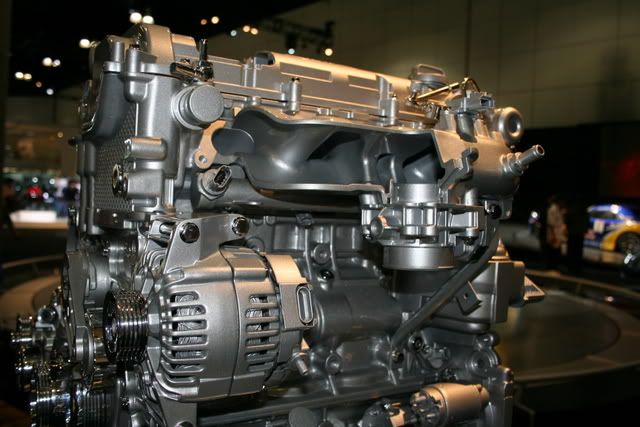
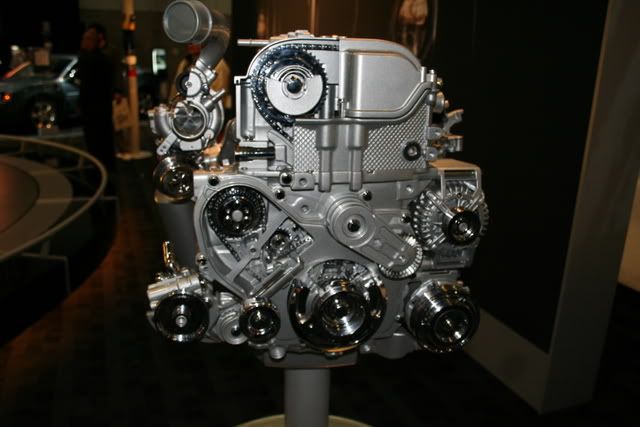


Last edited by ronn; 07-05-2011 at 01:49 AM.
#2
Good stuff. Shame there isn't an animation like this for the LNF:
YouTube - ‪Ecotec LSJ 2.0L Supercharger‬‏
YouTube - ‪Ecotec LSJ 2.0L Supercharger‬‏
#5
Yeah..but what the heck. All that stuff gets burried and you can't see it in a sticky anyore either. The link I showed actually has more info there..it's a great summary of the engine.
#6
very true very true.. I'm sure quite a few have overlooked it in the past. It has also been a while since it was posted so I'm sure it's still a new read for some members. Repost or not, there is still good info in there
Thread
Thread Starter
Forum
Replies
Last Post