Wanted to address some things about your Fuel System/Fuel Distribution
#26
The image that Doc attatched is almost identical to the LSJ fuel rail. If you look at the end there is a dampner being held on with 2 screws. I am willing to bet that removing those 2 screws and the cap will provide and opening to directly attatch a regulator and return line. Blown 4-banger and I have talked to a few Camaro/Corvette tuners and they agree with the concept of changing to a return setup with a boost referenced regulator. Blown should have it done on his car when he gets it re-assembled. We will see how that goes.
#27
im still learning about the cobalt and being deployed doesnt help my research any as im nowhere near my car! but anyways i was wondering... if GM wanted to make a Tuner car as is the SS/SC then why did they do a returnless fuel system? is it cheaper or what? wasnt the old setup sufficient enough in doing what its supposed to do? Also ive seen ALOT of turbo threads and i dont have the time to ravage through all of them... i did however try to of course... but is this returnless line one of the reasons other then the ECU on the 05-06 L61 why the Turbo setup is so hard to come up with?
#28
Most cars nowadays use a returnless system because of emissions problems with the return system. That, and it is cheaper to make than a return system as well.
This is interesting to read his thoughts on it though. I'm not sure about the #4 getting starved, though I do think that could be a possibility with the guys running the 60# injectors...
If someone has the physical dimensions of the fuel lines and the rail, I'm sure someone could figure out if there is enough fuel being pushed into all of the injectors.
This is interesting to read his thoughts on it though. I'm not sure about the #4 getting starved, though I do think that could be a possibility with the guys running the 60# injectors...
If someone has the physical dimensions of the fuel lines and the rail, I'm sure someone could figure out if there is enough fuel being pushed into all of the injectors.
#29
Hey awesome i just happen to have a brand new regulated fuel rail off a 2.2. I got it from a replacement engine i put in and used the old rail.
Got this from SI to throw it out there:
Fuel Pressure Regulator
The fuel pressure regulator is contained in the fuel sender assembly. The fuel pressure regulator is a diaphragm relief valve. The diaphragm has fuel pressure on one side and regulator spring pressure on the other side. Fuel pressure is controlled by a pressure balance across the regulator. The fuel system pressure is constant and is no longer a function of engine load or manifold vacuum. A software bias compensates the injector on-time based on the signal from the manifold absolute pressure (MAP) sensor.
The fuel rail assembly attaches to the cylinder head. The fuel rail assembly performs the following functions:
Positions the injectors in the cylinder head
Distributes fuel evenly to the injectors
Integrates the fuel pulse dampener into the fuel metering system
Got this from SI to throw it out there:
Fuel Pressure Regulator
The fuel pressure regulator is contained in the fuel sender assembly. The fuel pressure regulator is a diaphragm relief valve. The diaphragm has fuel pressure on one side and regulator spring pressure on the other side. Fuel pressure is controlled by a pressure balance across the regulator. The fuel system pressure is constant and is no longer a function of engine load or manifold vacuum. A software bias compensates the injector on-time based on the signal from the manifold absolute pressure (MAP) sensor.
The fuel rail assembly attaches to the cylinder head. The fuel rail assembly performs the following functions:
Positions the injectors in the cylinder head
Distributes fuel evenly to the injectors
Integrates the fuel pulse dampener into the fuel metering system
#30
I just got done reading all this very good info Got a question?
1) What if we upgrade our regulator and/or fuel rail, or a better Fuel Pump?
Lets not forget about ----> Pascal's law, Pascal's law of fluid pressures
pressure applied anywhere to a body of fluid causes a force to be transmitted equally in all directions; the force acts at right angles to any surface in contact with the fluid; "the fuel press is an application of Pascal's law"
Has anyone taken this into concideration?
1) What if we upgrade our regulator and/or fuel rail, or a better Fuel Pump?
Lets not forget about ----> Pascal's law, Pascal's law of fluid pressures
pressure applied anywhere to a body of fluid causes a force to be transmitted equally in all directions; the force acts at right angles to any surface in contact with the fluid; "the fuel press is an application of Pascal's law"
Has anyone taken this into concideration?
#31
Lets not get too caught up on the whole returnless thing as being a "problem". With a constant fuel pressure at the rail, fuel is simply controlled via modulating injector pulse width. Honestly, its like having one less variable to have to worry about.
#33
Good post for sure. We are currently also working on a solution. I have some bar stock rail that we have been playing around with and testing out. A larger rail will help the pressure drop also. Hopefully we will see some good results from it. Another option that may help is the aeromotive inline pump with the aeromotive fmu.
#34
Perhaps it could be the intake plenum that's causing part of the problem? VQ35DE's have the same problem in the 350Z's because of a poorly designed intake manifold. Some solutions that have proven successful with them are plenum spacers and even better redesigned flowing intake manifolds all together.
I have no clue about the construction and design of our manifolds but does anyone think this is a possibility? A flaw with our intake manifold (sharp turns and obstructions) causing cylinder 4 to run lean?
I have no clue about the construction and design of our manifolds but does anyone think this is a possibility? A flaw with our intake manifold (sharp turns and obstructions) causing cylinder 4 to run lean?
#36
i really want to read this, but its just so damn long! is this what you do at work all day adam?
and if it helps any, #4 cylinder is usually the cylinder to go on most ecotec engines, not just the 2.0's. in the past 2 years i've seen about 8 blocks where the #4 piston or rod just let go and destroyed the block, and this was in completly un modded cars. i dunno if that is relevant or not so ill let you decided while i read this
and if it helps any, #4 cylinder is usually the cylinder to go on most ecotec engines, not just the 2.0's. in the past 2 years i've seen about 8 blocks where the #4 piston or rod just let go and destroyed the block, and this was in completly un modded cars. i dunno if that is relevant or not so ill let you decided while i read this
#37
As you can see in this picture, the fuel comes from the driverside as halfcent said.. but actually dosen't enter the fuel rail there. It crosses the engine, and enters on the passenger side at the #1 cylinder.
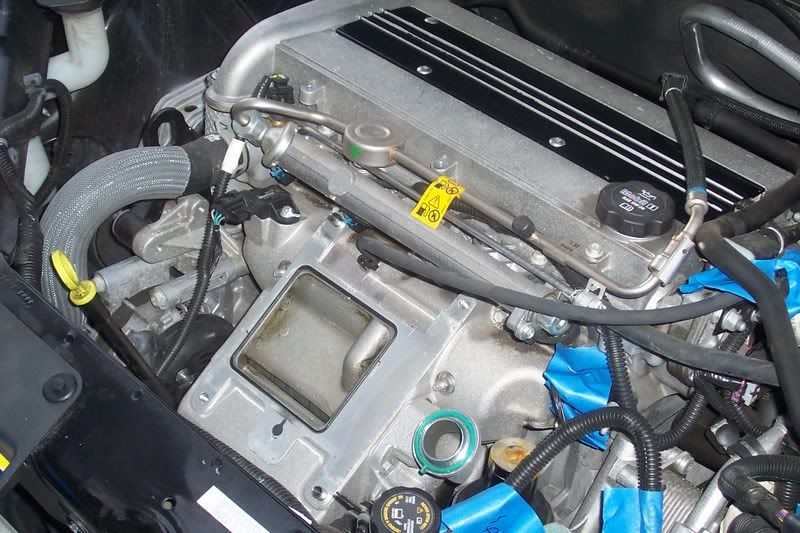
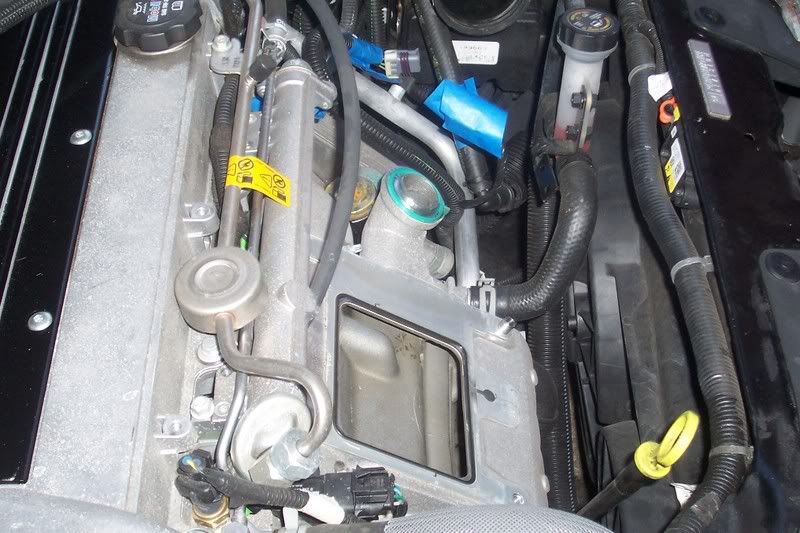
Very interesting post BTW. Subscribed.

#38
Oh, ok, Zinner and I just got done hijacking the crap outta a Hahn turbo post about this same topic, I didn't even see this thread.
Anyways, my 2 cents...
Adam, I believe the same you do about an uneven distribution of fuel pressure in the fuel rail with us who run 60lb-hr injectors. These are nearly double the stock flow and the fuel system and fuel rail imho was never designed to flow this amount of fuel. It lacks the capacity to act as a resevoir for flow changes thats needed to maintain a constant pressure and also probably acts as a restriction including the fuel filter, that will most likely show a pressure drop during high flow situations in the form of regulator pressure compared against rail pressure.
Your original post mentioned that a returnless style system variates pressure, thats not true. It holds a steady pressure regardless of engine load or manifold pressure.
As far as the fuel pump receiving a variable pulse width, we (ahem Zinner) found that isn't true. Ecotec fuel pumps run 100% duty cycle and recirculate fuel from the regulator back to the supply, however since the regulator is contained in tank, the excess fuel never leaves the tank and doesn't cause the evap problems that introduced returnless systems to begin with.
Also I thought I would just mention to clarify a topic that I see here a lot. Most injectors are rated for 45psi fuel pressure. Ecos usually run I believe ~60psi. I notice people think that because of that, our injectors will actually flow more than they are rated for and good for higher horsepower levels than normal, however this isn't true. Because we have returnless systems, the fuel pressure never increases over manifold pressure. If you run 20psi max manifold pressure, subtact that from fuel pressure, and you'll find what the injector is truly flowing. This is the entire purpose of an "Injector Flow Rate" table that we are all familiar with in HPTuners. It allows for the PCM to compensate for the high manifold pressure by commanding longer pulse widths from the injectors. That artificially high pulse width is to make up for the pressure the injector has to work against and takes away from available injector horsepower capacity. This effect pretty much triples the level of bullshit when it comes to properly sizing injectors. Normally, a 60 lb injector wouldn't have much trouble idling on a 4 cylinder with a return style system, because pressure would reduce at idle to a managable level, but on our cars, it remains at 60psi + manifold vacuum
. Now add the fact that in high boost situations, the injectors capacity is reduced because they are now being run at a much lower pressure over the manifold. So what happens is high effective injector pressure at idle, low effective pressure at WOT, tuning nightmare on both ends of the spectrum.
Switching to a return style system allows for an injector size that will both support high horsepower applications and also function better at idle or high rpm/low map conditions. The IFR table would simply be changed to all the same values, since the injector flow would rise in proportion to manifold pressure.
Anyways, my 2 cents...
Adam, I believe the same you do about an uneven distribution of fuel pressure in the fuel rail with us who run 60lb-hr injectors. These are nearly double the stock flow and the fuel system and fuel rail imho was never designed to flow this amount of fuel. It lacks the capacity to act as a resevoir for flow changes thats needed to maintain a constant pressure and also probably acts as a restriction including the fuel filter, that will most likely show a pressure drop during high flow situations in the form of regulator pressure compared against rail pressure.
Your original post mentioned that a returnless style system variates pressure, thats not true. It holds a steady pressure regardless of engine load or manifold pressure.
As far as the fuel pump receiving a variable pulse width, we (ahem Zinner) found that isn't true. Ecotec fuel pumps run 100% duty cycle and recirculate fuel from the regulator back to the supply, however since the regulator is contained in tank, the excess fuel never leaves the tank and doesn't cause the evap problems that introduced returnless systems to begin with.
Also I thought I would just mention to clarify a topic that I see here a lot. Most injectors are rated for 45psi fuel pressure. Ecos usually run I believe ~60psi. I notice people think that because of that, our injectors will actually flow more than they are rated for and good for higher horsepower levels than normal, however this isn't true. Because we have returnless systems, the fuel pressure never increases over manifold pressure. If you run 20psi max manifold pressure, subtact that from fuel pressure, and you'll find what the injector is truly flowing. This is the entire purpose of an "Injector Flow Rate" table that we are all familiar with in HPTuners. It allows for the PCM to compensate for the high manifold pressure by commanding longer pulse widths from the injectors. That artificially high pulse width is to make up for the pressure the injector has to work against and takes away from available injector horsepower capacity. This effect pretty much triples the level of bullshit when it comes to properly sizing injectors. Normally, a 60 lb injector wouldn't have much trouble idling on a 4 cylinder with a return style system, because pressure would reduce at idle to a managable level, but on our cars, it remains at 60psi + manifold vacuum

Switching to a return style system allows for an injector size that will both support high horsepower applications and also function better at idle or high rpm/low map conditions. The IFR table would simply be changed to all the same values, since the injector flow would rise in proportion to manifold pressure.
#39
Most cars nowadays use a returnless system because of emissions problems with the return system. That, and it is cheaper to make than a return system as well.
This is interesting to read his thoughts on it though. I'm not sure about the #4 getting starved, though I do think that could be a possibility with the guys running the 60# injectors...
If someone has the physical dimensions of the fuel lines and the rail, I'm sure someone could figure out if there is enough fuel being pushed into all of the injectors.
This is interesting to read his thoughts on it though. I'm not sure about the #4 getting starved, though I do think that could be a possibility with the guys running the 60# injectors...
If someone has the physical dimensions of the fuel lines and the rail, I'm sure someone could figure out if there is enough fuel being pushed into all of the injectors.
#40
Oh, ok, Zinner and I just got done hijacking the crap outta a Hahn turbo post about this same topic, I didn't even see this thread.
Anyways, my 2 cents...
Adam, I believe the same you do about an uneven distribution of fuel pressure in the fuel rail with us who run 60lb-hr injectors. These are nearly double the stock flow and the fuel system and fuel rail imho was never designed to flow this amount of fuel. It lacks the capacity to act as a resevoir for flow changes thats needed to maintain a constant pressure and also probably acts as a restriction including the fuel filter, that will most likely show a pressure drop during high flow situations in the form of regulator pressure compared against rail pressure.
Your original post mentioned that a returnless style system variates pressure, thats not true. It holds a steady pressure regardless of engine load or manifold pressure.
As far as the fuel pump receiving a variable pulse width, we (ahem Zinner) found that isn't true. Ecotec fuel pumps run 100% duty cycle and recirculate fuel from the regulator back to the supply, however since the regulator is contained in tank, the excess fuel never leaves the tank and doesn't cause the evap problems that introduced returnless systems to begin with.
Also I thought I would just mention to clarify a topic that I see here a lot. Most injectors are rated for 45psi fuel pressure. Ecos usually run I believe ~60psi. I notice people think that because of that, our injectors will actually flow more than they are rated for and good for higher horsepower levels than normal, however this isn't true. Because we have returnless systems, the fuel pressure never increases over manifold pressure. If you run 20psi max manifold pressure, subtact that from fuel pressure, and you'll find what the injector is truly flowing. This is the entire purpose of an "Injector Flow Rate" table that we are all familiar with in HPTuners. It allows for the PCM to compensate for the high manifold pressure by commanding longer pulse widths from the injectors. That artificially high pulse width is to make up for the pressure the injector has to work against and takes away from available injector horsepower capacity. This effect pretty much triples the level of bullshit when it comes to properly sizing injectors. Normally, a 60 lb injector wouldn't have much trouble idling on a 4 cylinder with a return style system, because pressure would reduce at idle to a managable level, but on our cars, it remains at 60psi + manifold vacuum
. Now add the fact that in high boost situations, the injectors capacity is reduced because they are now being run at a much lower pressure over the manifold. So what happens is high effective injector pressure at idle, low effective pressure at WOT, tuning nightmare on both ends of the spectrum.
Switching to a return style system allows for an injector size that will both support high horsepower applications and also function better at idle or high rpm/low map conditions. The IFR table would simply be changed to all the same values, since the injector flow would rise in proportion to manifold pressure.
Anyways, my 2 cents...
Adam, I believe the same you do about an uneven distribution of fuel pressure in the fuel rail with us who run 60lb-hr injectors. These are nearly double the stock flow and the fuel system and fuel rail imho was never designed to flow this amount of fuel. It lacks the capacity to act as a resevoir for flow changes thats needed to maintain a constant pressure and also probably acts as a restriction including the fuel filter, that will most likely show a pressure drop during high flow situations in the form of regulator pressure compared against rail pressure.
Your original post mentioned that a returnless style system variates pressure, thats not true. It holds a steady pressure regardless of engine load or manifold pressure.
As far as the fuel pump receiving a variable pulse width, we (ahem Zinner) found that isn't true. Ecotec fuel pumps run 100% duty cycle and recirculate fuel from the regulator back to the supply, however since the regulator is contained in tank, the excess fuel never leaves the tank and doesn't cause the evap problems that introduced returnless systems to begin with.
Also I thought I would just mention to clarify a topic that I see here a lot. Most injectors are rated for 45psi fuel pressure. Ecos usually run I believe ~60psi. I notice people think that because of that, our injectors will actually flow more than they are rated for and good for higher horsepower levels than normal, however this isn't true. Because we have returnless systems, the fuel pressure never increases over manifold pressure. If you run 20psi max manifold pressure, subtact that from fuel pressure, and you'll find what the injector is truly flowing. This is the entire purpose of an "Injector Flow Rate" table that we are all familiar with in HPTuners. It allows for the PCM to compensate for the high manifold pressure by commanding longer pulse widths from the injectors. That artificially high pulse width is to make up for the pressure the injector has to work against and takes away from available injector horsepower capacity. This effect pretty much triples the level of bullshit when it comes to properly sizing injectors. Normally, a 60 lb injector wouldn't have much trouble idling on a 4 cylinder with a return style system, because pressure would reduce at idle to a managable level, but on our cars, it remains at 60psi + manifold vacuum

Switching to a return style system allows for an injector size that will both support high horsepower applications and also function better at idle or high rpm/low map conditions. The IFR table would simply be changed to all the same values, since the injector flow would rise in proportion to manifold pressure.
What you said makes perfect sense.
I'll actually give someone a rep point lol
#41
You have that backwards. Our systems keep a static pressure. An FMU, or more correctly, a rising rate fuel pressure regulator, changes fuel pressure to compensate for an increase in manifold pressure, however not at the same rate. An FMU is a tuning method that introduces additional fuel in lack of fueling modifications. They are used mainly on stock NA cars that are converted to forced induction.
#42


#43
#44
This could be some of the reason as to why GM likes our cars to run a bit on the rich side. Less worry about temperatures dipping down, and our cars leaning out. No messing up Cylinder #4 this way
#47
I only see one problem with this whole theory. But my idea may not be true. I will try to explain it how I see it.
In a confined space, such as the fuel rail the pressure is going to stay the same through out it. It will even out. You may say bah he is full of nonsense but hear me out.
If you blow into a balloon, is the pressure greater where the opening is because you blew into it?? or is it the same throughout the balloon.
I understand that the pressure can travel in waves but in a system that is constantly being pressurized it would drop off like that...
IDK, I don't have a solution, its just how I see things..
In a confined space, such as the fuel rail the pressure is going to stay the same through out it. It will even out. You may say bah he is full of nonsense but hear me out.
If you blow into a balloon, is the pressure greater where the opening is because you blew into it?? or is it the same throughout the balloon.
I understand that the pressure can travel in waves but in a system that is constantly being pressurized it would drop off like that...
IDK, I don't have a solution, its just how I see things..
#49
I just got done reading all this very good info Got a question?
1) What if we upgrade our regulator and/or fuel rail, or a better Fuel Pump?
Lets not forget about ----> Pascal's law, Pascal's law of fluid pressures
pressure applied anywhere to a body of fluid causes a force to be transmitted equally in all directions; the force acts at right angles to any surface in contact with the fluid; "the fuel press is an application of Pascal's law"
Has anyone taken this into concideration?
1) What if we upgrade our regulator and/or fuel rail, or a better Fuel Pump?
Lets not forget about ----> Pascal's law, Pascal's law of fluid pressures
pressure applied anywhere to a body of fluid causes a force to be transmitted equally in all directions; the force acts at right angles to any surface in contact with the fluid; "the fuel press is an application of Pascal's law"
Has anyone taken this into concideration?